Occupational Safety and Health
The ILO Constitution sets forth the principle that workers should be protected from sickness, disease and injury arising from their employment. Yet for millions of workers the reality is very different. The ILO estimates that 2.02 million people die each year from work-related accidents or diseases. A further 317 million people suffer from work-related diseases, and there are an estimated 337 million fatal and non-fatal work-related accidents per year.
The suffering caused by such accidents and illnesses to workers and their families is incalculable. In economic terms, the ILO has estimated that 4% of the world’s annual GDP is lost as a consequence of occupational diseases and accidents. Employers face costly early retirements, loss of skilled staff, absenteeism, and high insurance premiums due to work-related accidents and diseases. Yet many of these tragedies are preventable through the implementation of sound prevention, reporting and inspection practices (www.ilo.org)

respiratory protection
Dust: Formed by the breaking down of solid materials, normally when materials are altered. For example, sanding, cutting, grinding and brushing. In general, the smaller the dust particle the greater the hazard that it presents. Fibers from materials should also be treated as dusts.
Mist: Formed by processes that involve atomization (such as spraying, cleaning and cutting/grinding using coolants) and consist of tiny liquid droplets rather like steam in a bathroom.
Fume: Formed by the vaporization of a solid material by the application of intense heat. Extremely fine particulates are formed as the fume cools and condenses. Many processes form fume; such as smelting, pouring metals and many welding applications.
Vapour: A gaseous state formed by evaporation from substances that are normally either solid or liquid at room temperature. Generally released at room temperature (petrol, methylated spirits), many industrial processes, used in degreasing vaporize particularly quickly once heated.
Gas: An air like substance at room temperature. Gases can travel far very quickly.
Oxygen Deficiency/Enrichment: When an atmosphere is likely to contain less than 19% oxygen (or where conditions may exist in the future to cause this to happen); and in certain circumstances where the risk may be oxygen enrichment, which can lead to explosion and severe impairment of operatives.
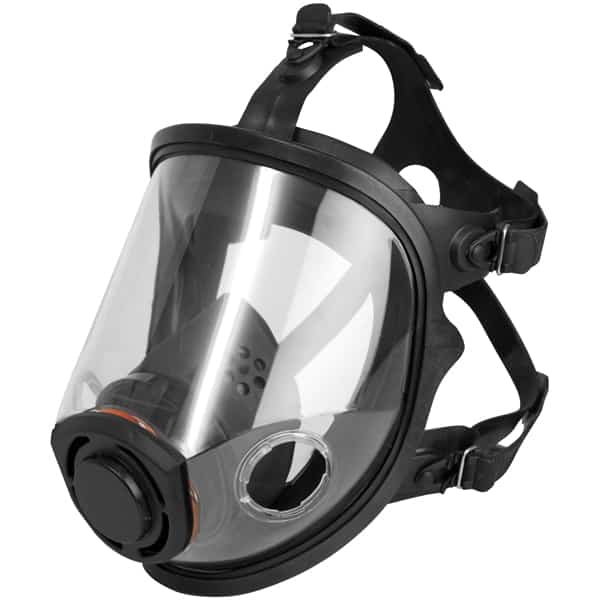
- Around 13,000 deaths every year from occupational lung disease and cancer
- Construction dust can cause irrepareble damage to lungs and airways
- Over 500 deaths every year from exposure to silica dust
- Around 400 deaths every year from COPD due to past workplace exposures

Body protection
Workers who face possible bodily injury of any kind that cannot be eliminated through engineering, work practice or administrative controls, must wear appropriate body protection while performing their jobs. In addition to cuts and radiation, the following are examples of workplace hazards that could cause bodily injury:
• Temperature extremes
• Hot splashes from molten metals and other hot liquids
• Potential impacts from tools, machinery and materials
• Hazardous chemicals.
EN standards for Body protection
EN342 Protective clothing against the cold (< -5°C)
EN343 Protective clothing against the rain
EN1149/5 Protection against the dangers caused by static electricity
EN ISO11611 Protective clothing for use in welding and allied processes
EN ISO 11612 (EN531) Protective clothing for workers exposed to heat (excluding fire- and welders clothing)
EN14605 Protection against liquid chemicals
EN14058 Protective clothing against cool environments
EN ISO14116 (EN533) Protective clothing with limited flame spread properties
EN ISO 20471 High-visibility clothing for professionals
EN61482-2 Protective clothing against the thermal hazards of an electric ARC
EN13034: Clothing for protection against liquid chemicals – Requirements for clothing that gives limited protection against liquid chemicals (Type 6 clothing)
hand protection
If a workplace hazard assessment reveals that workers face potential injury to hands and arms that cannot be eliminated through engineering and work practice controls, workers must wear appropriate protection. Potential hazards include skin absorption of harmful substances, chemical or thermal burns, electrical dangers, bruises, abrasions, cuts, punctures, fractures and amputations. Protective equipment includes gloves, finger guards and arm coverings or elbow-length gloves.
EN374-1 Protective gloves against dangerous chemicals and micro-organisms.


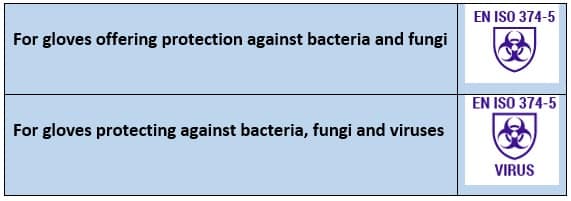
EN407 – Protective gloves against thermal risks (heat and/or fire)
The nature and degree of protection is shown by a pictogram followed by a series of six performance levels, relating to specific protective qualities. The higher the number, the better the test result. The following is tested:
a) Resistance to flammability
b) Resistance to contact heat
c) Resistance to convective heat
d) Resistance to radiant heat
e) Resistance to small splashed of molten metal
f) Resistance to large splashes of molten metal
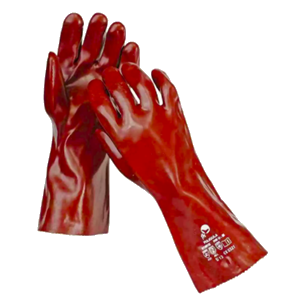
EN388 – Protective gloves against mechanical risks
Protection against mechanical hazards is expressed by a pictogram followed by 4 numbers (performance levels), each representing test performance against a specific hazards. Sometimes a 5th letter is added to indicate Cut resistance in accordance with ISO (A to F). The higher the number, the better the test result.
a) Resistance to abrasion (0 – 4)
b) Blade cut resistance (0 – 5)
c) Tear resistance (0 – 4)
d) Puncture resistance (0 – 4)
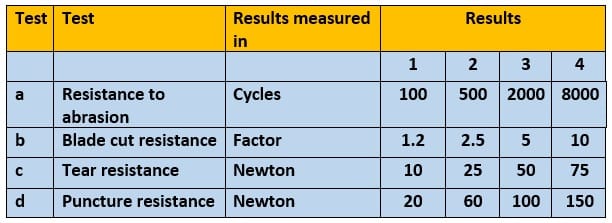


EN421 – Protective gloves against ionizing radiation and radioactive contamination
EN511 – Protective gloves against cold
EN659 – Protective gloves for firefighters
EN12477 – Protective gloves for welders
EN60903 – Protective gloves against electrical risks

Workers can be exposed to a large number of hazards that pose danger to their eyes and face. Workers need appropriate eye or face protection if they are exposed to eye or face hazards from flying particles, molten metal, liquid chemicals, acids or caustic liquids, chemical gases or vapors, potentially infected material or potentially harmful light radiation.
Many occupational eye injuries occur because of not wearing any eye protection while others result from wearing improper or poorly fitting eye protection.
Eye protection
Some of the most common types of eye and face protection include the following:
Safety spectacles: These protective eyeglasses have safety frames constructed of metal or plastic and impact-resistant lenses. Side shields are available on some models.
Goggles: These are tight-fitting eye protection that completely cover the eyes, eye sockets and the facial area immediately surrounding the eyes and provide protection from impact, dust and splashes. Some goggles will fit over corrective lenses.
Welding shields: Constructed of vulcanized fiber or fiberglass and fitted with a filtered lens, welding shields protect eyes from burns caused by infrared or intense radiant light; they also protect both the eyes and face from flying sparks, metal spatter and slag chips produced during welding, brazing, soldering and cutting operations. They require filter lenses to have a shade number appropriate to protect against the specific hazards of the work being performed in order to protect against harmful light radiation.
Face shields: These transparent sheets of plastic extend from the eyebrows to below the chin and across the entire width of the head. Some are polarized for glare protection. Face shields protect against nuisance dusts and potential splashes or sprays of hazardous liquids but will not provide adequate protection against impact hazards. Face shields used in combination with goggles or safety spectacles will provide additional protection against impact hazards.
EN Standards for Eye protection
EN166 – Personal eye protection
EN169 – Filters for welding and related techniques (Markings follow EN166. Contains informative annex giving guidance on selection and use of welding filters)
EN170 – Specifications for UV filters – Transmittance requirements
EN172 – Specifications for filters for protection against solar radiation, industrial use
EN175 – Eye and face protection during welding and allied processes
Eye protection – Frame Marking
Frame marking must include the CE symbol and manufacturer’s name (logo or brand). If the glasses refer to the EN standard, the EN standard number is mandatory together with the various use and mechanical strength symbols, in accordance with the tests requested by the manufacturer.
Symbols:
3. Liquid droplets or splashes.
4. Large dust particles > 5 microns.
5. Gas and fine dust particles < 5 microns.
8. Electrical short circuit arc.
9. Molten metal and hot solids.
Mechanical strength symbols:
S. Extra strong, resists a 22mm, 43 g ball falling 1.30m.at 5.1 m/s.
F. Low energy impact, resists a 6 mm, 0.86 g ball at 45 m/s.
B. Medium energy impact, resists a 6 mm, 0.86 g ball at 120 m/s.
A. High energy impact, resists a 6 mm, 0.86 g ball at 190 m/s.
Eye protection – Lens Marking
Lens marking must include the scale number of filtering lenses, the manufacturer’s name (logo or brand).
Optical class symbols:
1. Continuous work
2. Intermittent work
3. Occasional work, but must not be worn continuously.
Use symbols:
9. Molten metal and hot solids
Mechanical strength symbols:
S. Extra strong, resists a 22mm, 43 g ball falling 1.30m at 5.1 m/s
F. Low energy impact, resists a 6 mm, 0.86 g ball at 45 m/s.
B. Medium energy impact, resists a 6 mm, 0.86 g ball at 120 m/s.
A. High energy impact, resists a 6 mm, 0.86 g ball at 190 m/s.
K. Resistance to surface damage by fine particles (optional).
N. Resistance to fogging (optional)
T. The letter T, immediately after the mechanical strength symbol, authorizes use for high speed particles at extreme temperatures.
Head protection
Protecting workers from potential head injuries is a key element of any safety program. A head injury can impair a worker for life or it can be fatal. Wearing a safety helmet or bump cap is one of the easiest ways to protect from any head injury. Hard hats can protect workers from impact and penetration hazards as well as from electrical shock and burn hazards.
Wear head protection if any of the following apply:
- Objects might fall from above and strike the worker on the head;
- Workers might bump their heads against fixed objects, such as exposed pipes or beams; or
- There is a possibility of accidental head contact with electrical hazards.
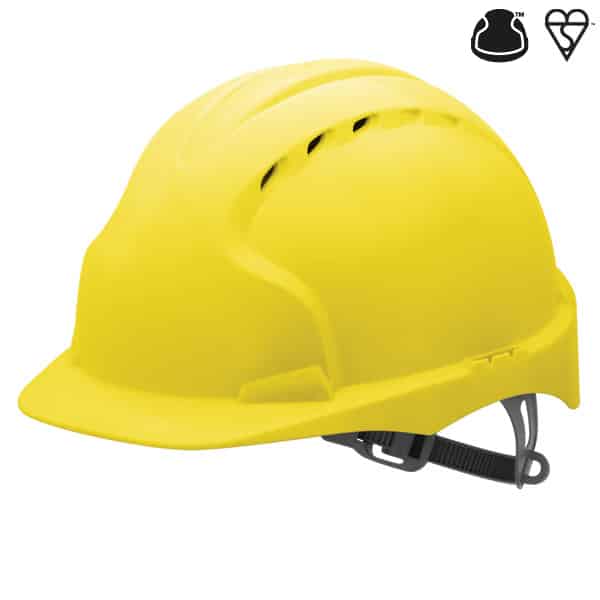
EN Standards for Head protection
EN14052 – HIGH PERFORMANCE INDUSTRIAL SAFETY HELMETS
The specification includes the requirement for side impact protection. Tests require that the shell is subjected to a total of150J of impact energy, 100J to the top of the helmet and 50J to the side (up to 60° from the crown) of the helmet. Penetration testing is also required with a “blade” striker being dropped from 2.5m to give an impact energy of 25J on to the top of the helmet and on to the side of the helmet with an impact energy of 20J from 2m.
EN12492 – MOUNTAINEERS HELMETS
A helmet complying to the mountaineering standard is impact tested with two 5kg strikers. A hemispherical striker is dropped from 2m onto the crown of the helmet and a flat striker from 500mm on to the front, rear or side by tilting the headform to 30°. In all cases, the transmitted force through the neck of the headform must not exceed 10kN. Two penetration tests with a 3kg pointed striker are also performed within a 50mm radius of the helmet’s crown without making contact with the headform. *Meets the shock absorption and impact test of EN397.
EN397 – INDUSTRIAL SAFETY HELMETS
This standard goes back over 50 years and testing is only carried out to the top of the helmet. A 49J impact only to the crown of the helmet measures the shock absorption and a penetration test with a 3kg conical striker from 1m. There is no side impact test in this standard only a lateral rigidity test, which is a slow, progressive force loading, and is not an impact test.
EN50365 – ELECTRICAL INSULATION FOR INDUSTRIAL SAFETY HELMETS
An additional specification for helmets used for working live installations up to 1000V. Testing is carried out at voltages of 10,000V (On non-vented). The EN50356 standard is marked on the helmet with a sticker.
EN812 – INDUSTRIAL BUMP CAPS
This specification requires the cap being hit four times by a 5kg flat steel striker falling with 12 Joules of energy. A bump cap is intended to provide protection against bumps and scrapes to the head, it should not be used where falling or thrown objects are likely and should not be used where an industrial safety helmet is required.

Hearing protection
Exposure to high levels of noise can cause permanent hearing loss. Neither surgery nor a hearing aid can help correct this type of hearing loss.
Construction sites have many noisy operations and can be a significant source of noise exposure. Loud noise can also reduce work productivity and contribute to workplace accidents by making it difficult to hear warning signals. Hearing loss from loud noise limits your ability to hear high frequencies, understand speech, and reduces your ability to communicate, which can lead to social isolation.
Hearing loss can affect your quality of life by interfering with your ability to enjoy socializing with friends, playing with your children or grandchildren, or participating in other activities. Damage to your hearing can be prevented, but once permanent noise-induced hearing loss occurs, it cannot be cured or reversed. Hearing loss usually occurs gradually, so you may not realize it is happening until it is too late.
EN Standards for Hearing protection
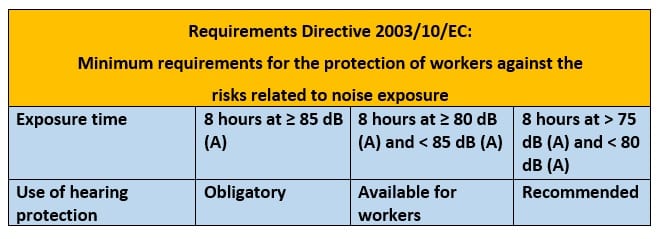
EN352-1 – Hearing protectors – Ear muffs
EN352-2 – Hearing protectors – Ear plugs
EN352-3 – Hearing protectors – Ear muffs attached to a safety helmet
EN352-6 – Hearing protectors – Ear muffs with electrical audio input
EN458 – Hearing protectors – Recommendations for selection, use, care and maintenance
SNR (Single Number Rating)
Levels of hearing protectors are commonly divided per SNR (Single Number Rating). SNR is only a general means of comparing different ear protectors. Generally the higher the SNR number the better the performance of the ear defender across a range of noise frequencies.

Foot protection
Workers who face possible foot or leg injuries from falling or rolling objects or from crushing or penetrating materials should wear protective footwear. Also, workers whose work involves exposure to hot substances or corrosive or poisonous materials must have protective gear to cover exposed body parts, including legs and feet.
EN20345 – Personal protective equipment – Safety footwear
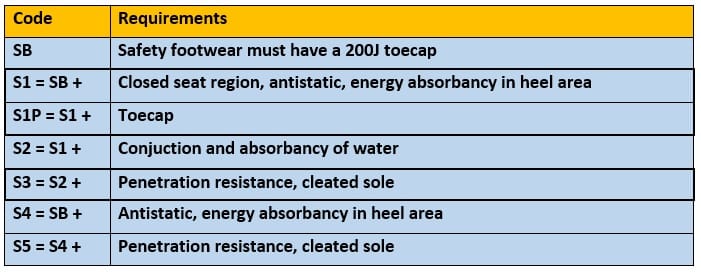

Safety shoes S1, S1P and S3 are the most sold types of safety shoes for the industry